Understanding UV Adhesion Primers: A Comprehensive Guide
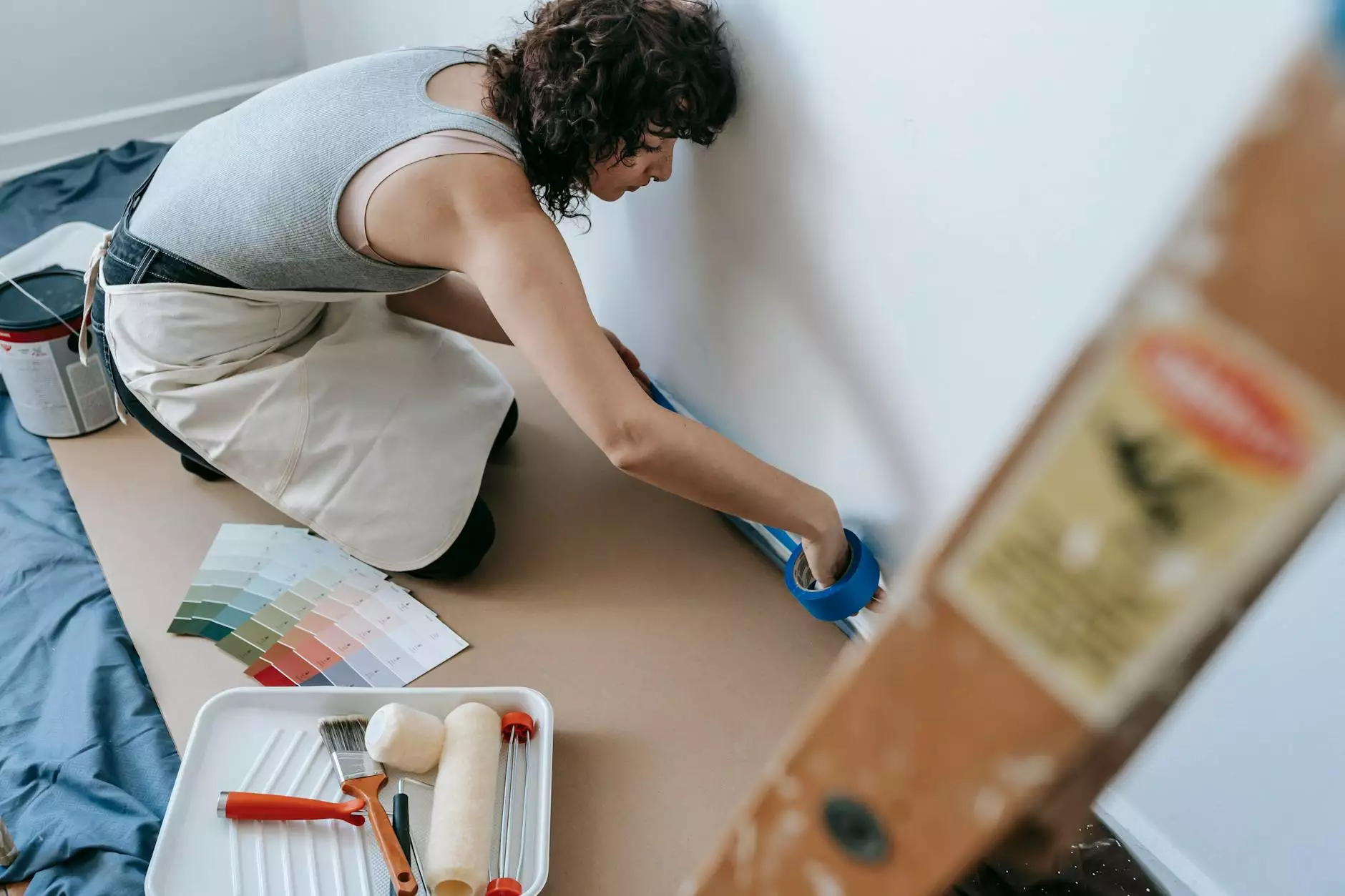
UV adhesion primers are essential components in the printing services industry, particularly when it comes to achieving superior print quality and durability. As businesses like Boston Industrial Solutions strive to enhance their offerings, understanding the intricacies of UV adhesion primers can significantly impact the final product.
What are UV Adhesion Primers?
UV adhesion primers are specialized coatings applied to substrates prior to the application of UV ink. Their primary function is to improve the adhesion of UV inks to various surfaces, ensuring a more robust and long-lasting print. These primers are especially valuable when working with non-porous materials, such as plastics, metals, and glass, where standard inks may struggle to adhere effectively.
The Chemistry Behind UV Adhesion Primers
Understanding the chemistry of UV adhesion primers is crucial for any business involved in printing services. These primers typically consist of a mixture of polymers, adhesion promoters, and solvents. Upon exposure to UV light, the primer undergoes a photochemical reaction, leading to a rapid curing process that bonds the primer to the substrate effectively. This ensures that the printed material withstands various environmental stresses such as moisture, chemicals, and abrasion.
Key Benefits of Using UV Adhesion Primers
- Enhanced Adhesion: The primary benefit of using UV adhesion primers is their ability to significantly enhance ink adhesion to challenging surfaces.
- Increased Durability: Prints created with UV inks over properly primed surfaces exhibit improved resistance to chipping, scratching, and environmental damage.
- Faster Production Times: UV curing is a rapid process, allowing for quicker production times compared to traditional printing methods.
- Versatility: These primers can be used on a wide variety of substrates, expanding the range of projects that printers can tackle.
- Improved Print Quality: By ensuring better adhesion, UV primers contribute to sharper, more vibrant prints that meet customer expectations.
Applications of UV Adhesion Primers
Industries across the board utilize UV adhesion primers in various applications. Here are some prominent examples:
1. Packaging Industry
In the packaging sector, UV adhesion primers are critical for printing on flexible films, labels, and cartons. They ensure that the graphics maintain their integrity throughout the supply chain, enhancing customer satisfaction.
2. Signage and Display
For businesses producing signs or promotional displays, adherence to substrates like acrylics and metals is vital. UV adhesion primers provide the necessary foundation for vibrant and long-lasting graphics.
3. Industrial Applications
Industrial printing often involves complex components where durability is essential. Primers designed for UV inks are essential in ensuring that prints withstand harsh environments and mechanical wear.
How to Choose the Right UV Adhesion Primer
Selecting the correct UV adhesion primer can significantly affect the outcome of your printing projects. Here are some key considerations:
- Substrate Compatibility: Ensure the primer is suitable for the material you are printing on.
- Ink Type: Consider whether you are using a standard UV ink or a specialty ink that may require a different formulation.
- Curing Method: Different primers may require specific UV curing equipment; therefore, compatibility with your current setup is crucial.
- Environmental Resistance: If prints are exposed to harsh conditions, choose primers that offer better resistance to chemicals and UV light.
Challenges and Solutions when Using UV Adhesion Primers
While UV adhesion primers offer numerous benefits, there can also be challenges in their use. Addressing these issues promptly can lead to better outcomes.
1. Surface Preparation
Improper substrate preparation can lead to inadequate adhesion. Always ensure surfaces are clean and free from contaminants prior to applying the primer.
2. Thickness of Application
Applying the primer too thin may not yield the desired adhesion, while too thick could result in a long curing time. Follow the manufacturer's recommendations for optimal results.
3. Curing Time
Insufficient curing can lead to poor adhesion. Verify that your UV curing system is functioning effectively, and adjust exposure times as necessary.
Future Trends in UV Adhesion Primers
As the printing industry evolves, so does the technology surrounding UV adhesion primers. Some trends to watch include:
- Sustainability: There is a growing demand for eco-friendly primers that reduce the environmental impact of printing processes.
- Advanced Formulations: Research continues into developing primers that provide even better adhesion and performance across a broader range of materials.
- Aging Resistance: Formulations that enhance resistance to aging and degradation from environmental exposure will likely become more prevalent.
Conclusion
In conclusion, UV adhesion primers play a pivotal role in enhancing print quality and durability in the printing services industry. Businesses like Boston Industrial Solutions stand to gain significantly by incorporating these primers into their production processes. By understanding their chemistry, benefits, applications, and future trends, companies can better position themselves in a competitive market and meet the ever-changing demands of customers.
By leveraging the detailed information provided in this guide, businesses can not only elevate their printing services but also ensure exceptional outcomes in every project.